Introduction
In customizing PET bottle molds, bottle design, neck size, and weight control are key factors that impact product market competitiveness, production costs, and equipment compatibility. As a PET blow molding machine and mold manufacturer with 20 years of experience, we produce over 2,000 molds annually, collaborating with a vast number of clients and gaining extensive practical knowledge. In particular, when serving startups, we’ve observed a tendency to focus on aesthetic design while overlooking production feasibility, often resulting in design revisions or production obstacles. This article will examine five aspects—consumer acceptance, production standards, labeling methods, equipment compatibility, and weight selection—to help you develop a mold solution that meets both market demand and filling equipment requirements.
1. Consumer Acceptance: How Does Design Impact Market Performance?
Consumer acceptance determines the market success of a bottle’s design. There are numerous PET bottle designs on the market; major brands such as Coca-Cola and Pepsi have retained their classic bottle designs for decades to strengthen brand recognition among consumers. In contrast, smaller brands tend to emulate mainstream bottle designs to reduce design costs and boost market acceptance.
Table 1: Comparison of Bottle Designs Between Major Brands and Small Brands
Brand | Design Characteristics | Replacement Frequency | Consumer Response |
---|---|---|---|
Coca-Cola | Signature curved bottle | Rarely changed | Strong consumer recognition |
Pepsi | Standard round shape | Stable design | High brand loyalty |
Small Brands | Modified popular designs | Regularly adjusted | Improved brand acceptance |
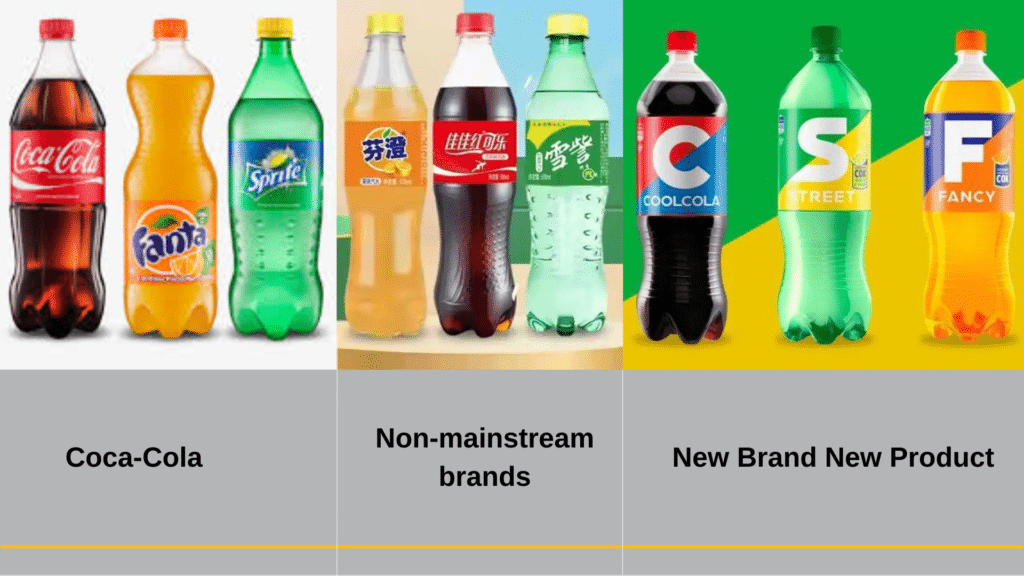
2. Production Standards: How to Balance Design and Production Requirements?
2.1 Complex Designs vs. Production Feasibility
Overly complex designs can introduce technical challenges in mold production and the manufacturing process. For example, a client from Thailand wanted to engrave a complex dragon pattern covering 2/3 of the bottle surface. Due to the depth and complexity of the design, high rejection rates occurred during demolding. Typically, mold pattern depths should not exceed 1 mm to ensure mold feasibility while achieving desired decorative effects.
Table 2: Mold Pattern Depth and Demolding Difficulty
Pattern Depth (mm) | Demolding Difficulty | Pass Rate | Rejection Rate |
---|---|---|---|
0.5 - 1.0 | Low | High | Low |
Above 1.0 | High | Lower | High |

3. Neck Size Selection: The Importance of Matching Filling Equipment
Different filling machines have unique neck size standards, and mismatched neck designs and equipment will disrupt production. This is particularly relevant for companies that rely on outsourcing production, as knowing the neck size standards of their contract manufacturers in advance can prevent production delays due to incompatibility.
4. Choosing the Right Labeling Method
The labeling method dictates the designated label area on the bottle. The two primary PET bottle labeling methods are sticker labels and shrink sleeves. Shrink-sleeved bottles must ensure that bottle diameters align with label dimensions, while sticker-labeled bottles require flat areas. Confirming label dimensions and methods in advance can prevent label misalignment issues after mold production.
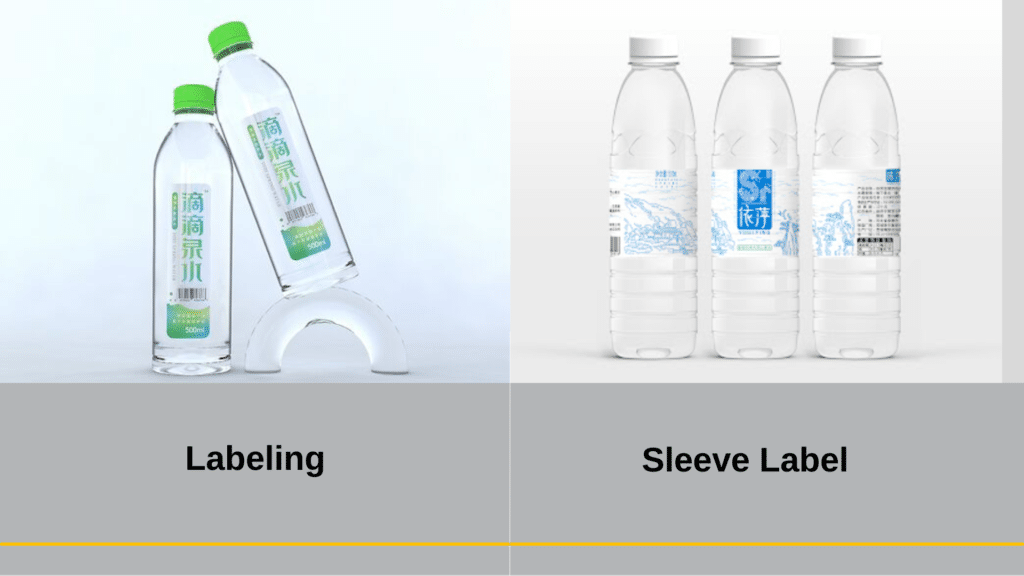
5. Matching Blow Molding Machines and Mold Design
In bottle design, the bottle’s height, diameter, and neck size must fit within the blow molding machine’s stroke and neck diameter range. If the dimensions exceed equipment specifications, mold installation and production will be impossible. Clients should carefully check equipment specifications before finalizing design plans to avoid production delays due to oversized designs.
Table 3: Examples of Blow Molding Machine Specifications and Applicable Bottle Designs
Blow Molding Machine Model | Max Stroke (mm) | Max Neck Diameter (mm) | Applicable Bottle Size (ml) |
---|---|---|---|
Model 2L | 250 | 30 | 0-2000 |
Model 20L | 350 | 70 | 2000-20000 |
Model 40L | 500 | 130 | 10000-40000 |
6. Selecting the Appropriate Weight
Bottle weight directly impacts production costs. For companies with high production volumes, reducing the preform weight can significantly cut material costs.
6.1 Fixed Bottle Design: Weight Calculation
When the bottle design is finalized, designers will calculate the theoretical preform weight based on the design. For instance, a 500 ml bottle with a 3025 neck typically requires an 18-gram preform, allowing companies to select a preform specification that fits within this weight range.
6.2 Cost-Driven Weight Reduction Design Optimization
Experienced clients often prioritize preform weight, focusing on maintaining strength while reducing weight. For example, reducing the preform weight by 4.5 grams can save 10.8 tons of raw material annually, significantly lowering production costs in a highly competitive market.
Table 4: Cost Savings from Weight Optimization
Monthly Production Volume (bottles) | Weight Reduction (grams) | Raw Material Saved (kg) | Annual Savings (tons) |
---|---|---|---|
200,000 | 4.5 | 900 | 10.8 |
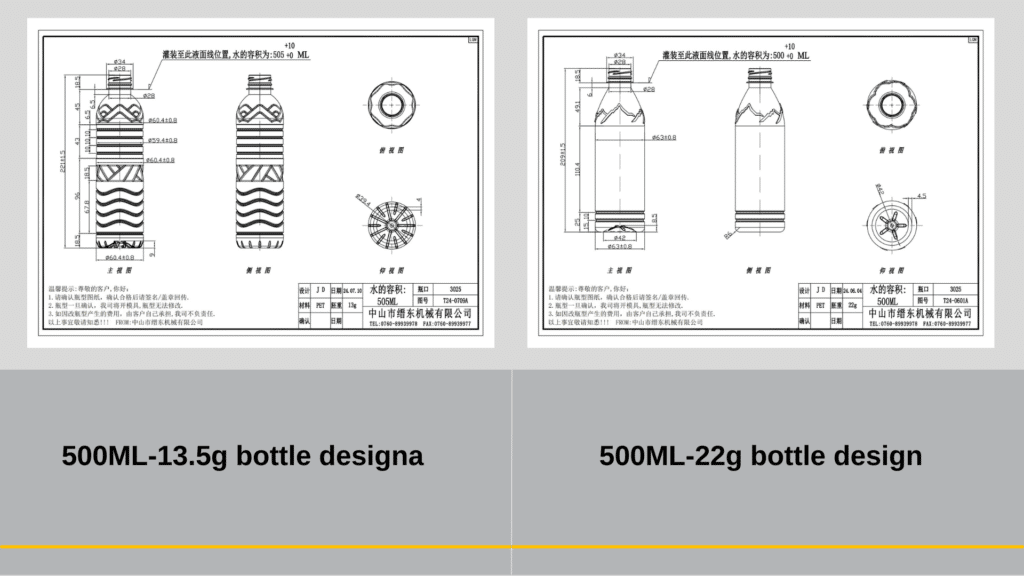
Case Study: Differences in Bottle Design Between Startups and Experienced Customers
Our data shows that startups often spend considerable time on design, with average communication lasting 3-4 hours and requiring over 4 design revisions. In contrast, experienced clients can clarify design requirements in just 5 minutes, lowering design and communication costs.
Table 5: Design Communication Time Comparison Between Startups and Experienced Clients
Client Type | Average Communication Time (hours) | Number of Revisions | Time to Finalize Design |
---|---|---|---|
Startups | 3-4 | 4+ | Long |
Experienced | 0.5 | 1-2 | Short |
Conclusion: Choosing the Right Mold to Meet Market and Equipment Needs
When designing bottle molds, clients should consider consumer acceptance, production standards, and equipment specifications. A thoughtful design can enhance market appeal and control production costs effectively. As a Chinese manufacturer with 20 years of experience, we specialize in high-quality PET blow molding machines and molds, helping clients gain a competitive edge in the market. For more information, visit our website: www.ibottler.com.
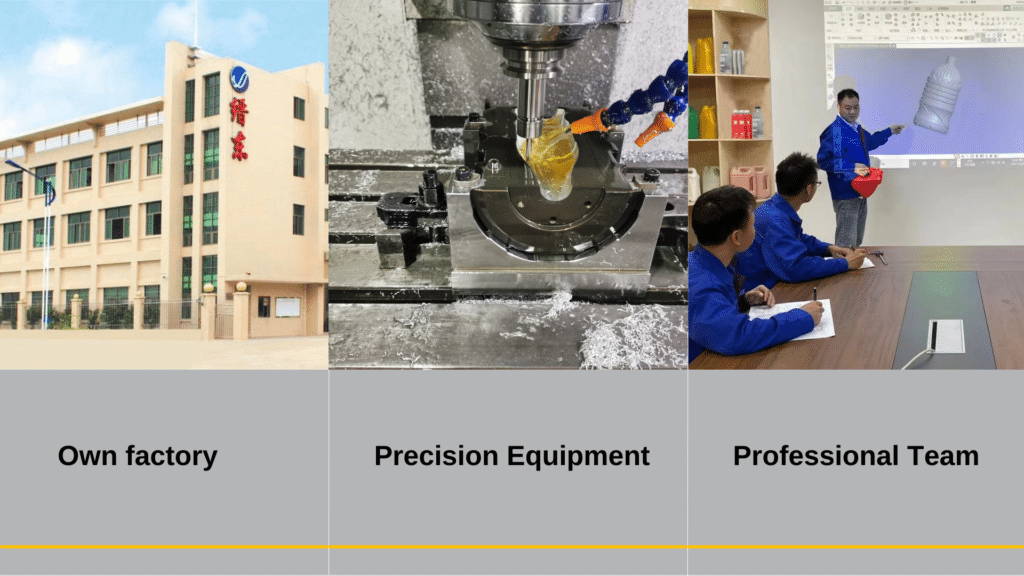