How Startups Can Reduce Production Costs with a 2-Cavity Semi-Automatic Blow Molding Machine
Introduction
As blow molding machines become more automated, certain high-end models achieve outputs of up to 36,000 bottles per hour. Yet, many startups still opt for the 2-cavity semi-automatic blow molding machine. Why? It boils down to two major factors: cost control and ease of operation. This article explores the benefits and limitations of the 2-cavity semi-automatic blow molding machine, comparing it with the 2-cavity automatic model to help companies decide which best fits their needs.
Cost Comparison: Semi-Automatic vs. Automatic Blow Molding Machines
Machine Type | Price (USD) | Hourly Output (Bottles) | Power Consumption | Floor Space (㎡) |
---|---|---|---|---|
2-Cavity Semi-Auto | 9,500 | 1,000 | Lower | 8-10 |
2-Cavity Automatic | 27,000 | 2,000 | Higher | ≥50 |
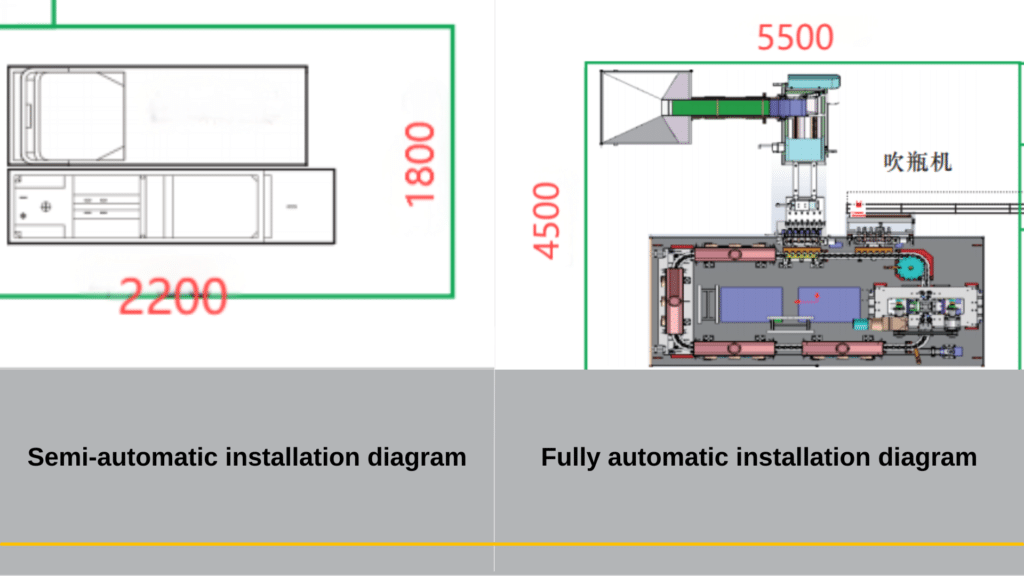
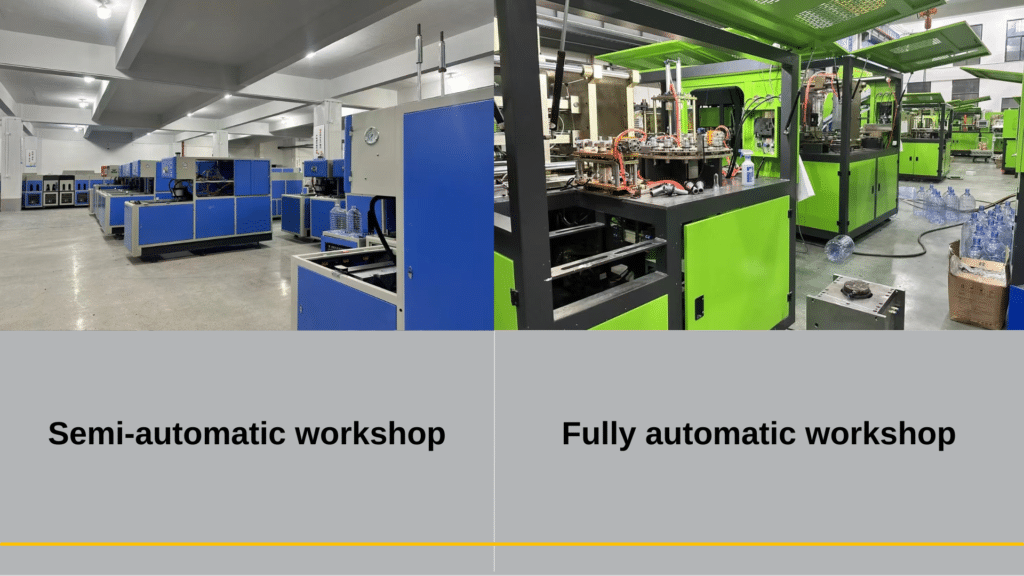
- Equipment Cost and Production Capacity
Semi-automatic machines cost around one-third of an automatic model with double the output but twice the energy consumption. For example, with 500mL bottles, a semi-automatic machine produces 1,000 bottles per hour, while the automatic reaches 2,000. The semi-automatic option also requires less space, only 8-10㎡, compared to the 50㎡ minimum for the automatic version. - Labor Cost
The semi-automatic machine requires only one worker, whose monthly wage is approximately 5,000 RMB (about 680 USD), while an experienced operator for the automatic machine earns around 8,000 RMB (1,090 USD). For startups, this lower labor cost significantly reduces operating expenses.
Investment Analysis for Producing 500mL Bottles
Before choosing equipment, startups should calculate the production cost of a 500mL bottle. Here is an example based on the monthly output of a semi-automatic machine:
Item | Quantity | Unit Cost (USD) | Total Cost (USD) |
---|---|---|---|
Preforms (18g) | 200,500 | 0.027 | 5,413.5 |
Labor | 1 worker | 680 | 680 |
Energy (Estimate) | - | 0.014/bottle | 2,800 |
Total | - | - | 8,893.5 |
The current price of a 500ml PET bottle sold online is around 0.80-0.1, which can be used as a reference.
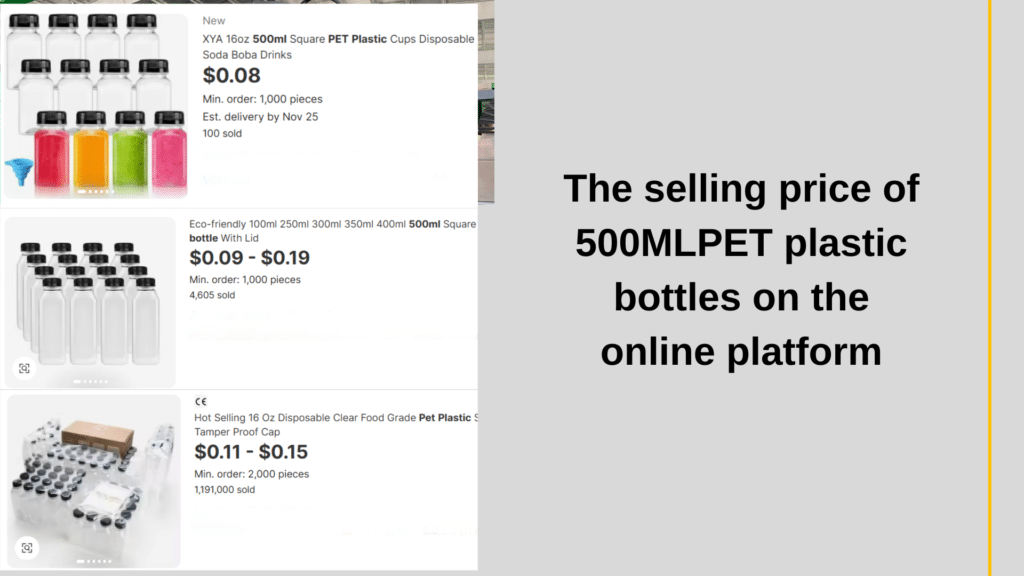
Initial Investment Comparison: Semi-Automatic vs. Automatic
Item | Semi-Automatic (USD) | Automatic (USD) |
---|---|---|
Equipment | 9,500 | 27,000 |
Preforms (18g) | 5,413.5 | 10,800 |
Installation Fee | 200-500 | 1,000-1,500 |
Total | 15,113.5 | 39,300 |
For startups, the lower initial investment required for a semi-automatic machine reduces risk, aligning with a cost-efficient strategy.
Operational and Maintenance Complexity
Due to its simpler design, the semi-automatic blow molding machine is ideal for startups with limited experience.
Aspect | Semi-Automatic | Automatic |
---|---|---|
Internal Structure | Basic parts: cylinders, valves | Hundreds of pneumatic components |
Troubleshooting | Easy to maintain, parts replacement | Complex, requires experienced operators |
Operation | Simple, manual loading/unloading | Fully automated, requires programming |
Semi-automatic machines’ simple structure allows most users to quickly resolve 90% of issues by replacing key components such as cylinders and valves. In contrast, automatic machines are more complex, with hundreds of pneumatic parts that can make troubleshooting difficult without experienced operators.
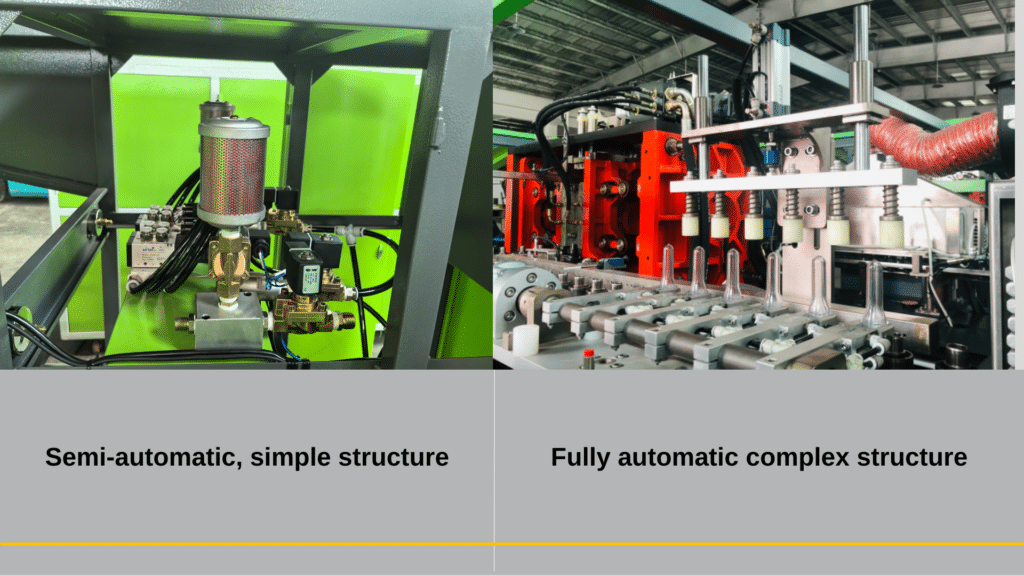
Case Study Analysis
Many startups report that automatic machines’ installation and setup are costly due to the need for on-site technical support. In contrast, semi-automatic machines are easily set up by the customer with instructional videos.
Installation Aspect | Semi-Automatic | Automatic |
---|---|---|
Installation Time | Half a day | 2-3 days |
Engineer Fee | None | 100-150 USD/day |
Total Installation Cost | 200-500 USD | 1,000-1,500 USD |
Profit Recovery Estimate
Using a 2-cavity semi-automatic machine to produce 500mL bottles, a startup could recover their initial costs within 4-6 months. Assuming a per-bottle cost of 0.048 USD (materials, labor, and utilities), a selling price of 0.08-0.10 USD yields a gross profit per bottle of 0.032-0.052 USD. After deducting platform commissions and other fees, the net profit per bottle would be around 0.03 USD, providing monthly profits of roughly 6,000 USD.
Conclusion: Why Choose a Semi-Automatic Blow Molding Machine?
From ease of operation to cost control and simpler maintenance, the 2-cavity semi-automatic blow molding machine is an optimal choice for startups with limited funds and experience. As the company gains experience and resources, upgrading to a fully automated production line becomes a feasible next step.
About Us
We are a 20-year-old factory in China specializing in PET blow molding machines, blow molds, and preform molds. For more information on our products and services, please visit our website:https://ibottler.com/