Meta Description: How to avoid mismatched dimensions when ordering molds? Understand the difference between bottle design and mold installation drawings, grasp essential data, and ensure the mold aligns with your blow molding machine for smooth production.
Introduction: Why is Precision in Mold Dimensions Essential?
When reordering blow molds, many factories encounter issues with mismatched mold dimensions and blow molding machine installations, leading to production interruptions and quality issues. To ensure smooth installation of new molds, it is essential to understand the difference between bottle design drawings and mold installation drawings and to confirm key dimensional data, as this will help prevent common fitting problems.
Bottle Design Drawings ≠ Mold Installation Drawings
Many clients mistakenly believe that bottle design drawings (i.e., 2D bottle design and 3D renderings) are enough for ordering molds. While these drawings do display the bottle's appearance dimensions, they do not account for the actual installation requirements of the mold. The mold installation drawings include crucial details like mold thickness, center distance, water structure, and bottom installation method, which are all essential for the mold to fit the blow molding machine properly.
Table 1: Differences Between Bottle Design Drawings and Mold Installation Drawings
Drawing Type | Meaning | Primary Purpose | Common Misconception |
---|---|---|---|
Bottle Design (2D/3D) | Shows the bottle's appearance dimensions (height, width, etc.) | Ensures the bottle’s visual design | Believing bottle design drawings alone are sufficient for mold compatibility |
Mold Installation | Contains essential installation data (thickness, center distance, etc.) | Ensures seamless mold installation | Not requesting mold installation drawings leads to incompatible molds |
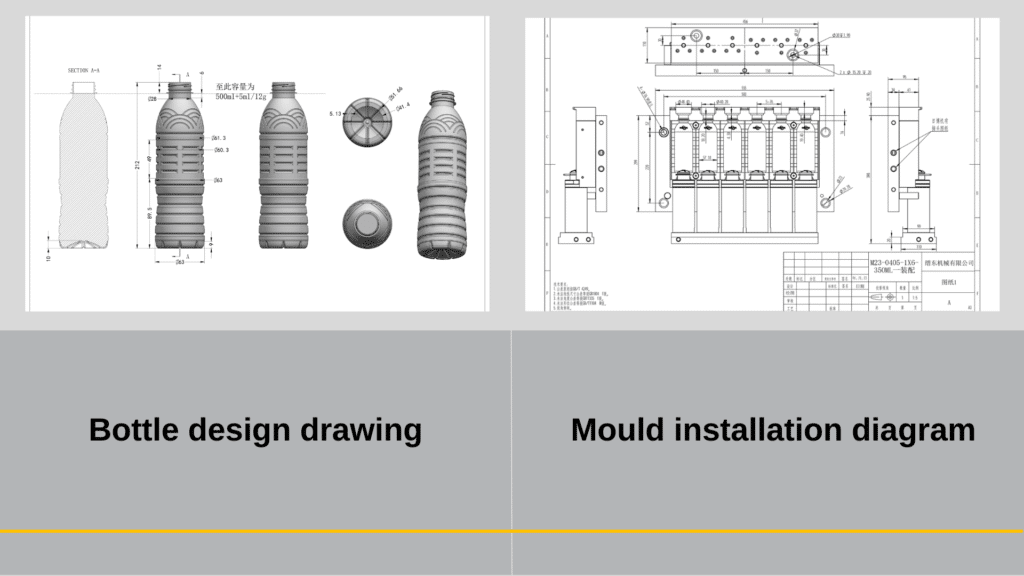
Key Mold Data and Common Problems in Installation
During mold installation, the following key data points are crucial. Any deviation in these values can lead to mold incompatibility or affect product quality. The table below highlights some common data points and their potential impact on production.
Table 2: Key Mold Data and Their Corresponding Problems
Data Item | Description | Common Problem | Impact |
---|---|---|---|
Mold Thickness | Ensures compatibility with equipment stroke | Incorrect thickness leads to improper mold clamping | Poor sealing, leading to leaks and unstable formation |
Center Distance | Ensures proper alignment of bottle cavities with equipment’s stretch rods | Misaligned stretch rods hinder bottle formation | Misaligned bottle formation, impacting appearance and quality |
Water Structure | Cooling design within the mold to maintain stable temperatures | Lack of water circulation overheats mold, distorting bottles | Lower product quality, increased mold wear |
Bottom Installation Method | Bottom angle and mounting style suited to equipment structure | Incompatible bottom installation affects stability | Unstable mold mounting, reducing production efficiency |
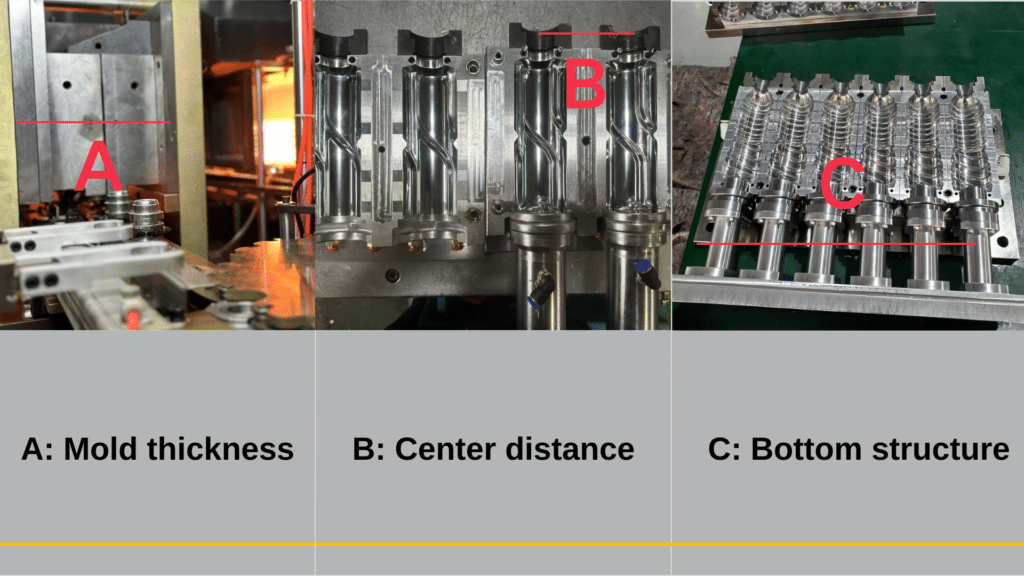
Case Analysis: Real Issues Caused by Dimension Mismatch
Case 1: Production Halt Due to Mold Thickness Discrepancy
A customer’s mold, designed for an automatic blow molding machine, had excess thickness, preventing it from clamping correctly. As the machine could not adjust for the mold thickness, the customer had to reduce the thickness manually, which was time-consuming and reduced the mold’s lifespan. Accurate thickness data would have prevented this issue.
Case 2: Deformed Bottles Due to Lack of Water Structure
A South African customer bought a mold via a trading company, but the mold lacked an internal water-cooling design. After only a few bottles, the mold overheated, causing bottle deformation. Ultimately, the client had to replace the mold, incurring extra time and expense.
Case 3: Misalignment from Incorrect Center Distance
Another customer’s mold was incompatible due to a center distance mismatch with the machine, preventing the stretch rods from aligning properly with the bottle cavities. The customer had to reorder the mold, causing production delays and extra costs.
These cases highlight the importance of accurate key data to ensure smooth production. Hence, it’s crucial to verify every dimension on the installation drawing before production.
Solution: How to Ensure Accurate Mold Dimensions?
To avoid issues with dimension mismatch, the following steps are recommended:
- Verify Key Data in Advance: When purchasing a mold, list all essential data points, including mold thickness, center distance, water structure, and bottom installation method.
- Secure Mold Installation Drawings: Bottle design drawings are insufficient for compatibility. Ensure the mold installation drawing includes all installation data and verify its accuracy before production.
- Select the Right Mold Material: The material significantly impacts mold quality and durability. We recommend using aircraft-grade aluminum molds for enhanced durability and optimal heat dissipation.
- Conduct Multiple Data Checks and Measurement Support: We have mold data for over 90% of major brands (SIDEL, SACMI, SIPA, etc.), which enables data cross-checking for precise alignment with your machine. For less common brands, we provide a blank mold data form for clients to measure and fill out, ensuring data accuracy.
Table 3: Mold Pre-Purchase Checklist
Checklist Item | Description | Expected Outcome |
---|---|---|
Mold Thickness Check | Ensure thickness matches equipment requirements | Avoids manual thinning, ensuring mold clamping |
Center Distance Check | Confirm center distance aligns with equipment stretch rod positioning | Ensures bottles are correctly positioned |
Water Structure Check | Verify water-cooling system design | Maintains temperature control, improving bottle quality |
Bottom Installation Check | Confirm bottom mounting aligns with equipment structure | Ensures stable installation, facilitating efficient production |
Material Selection | Choose durable, thermally conductive materials (e.g., aircraft aluminum) | Extends mold lifespan, reduces maintenance costs |
Review of Installation Drawings | Obtain and verify comprehensive installation drawings | Ensures dimension compatibility, avoiding production interruptions |
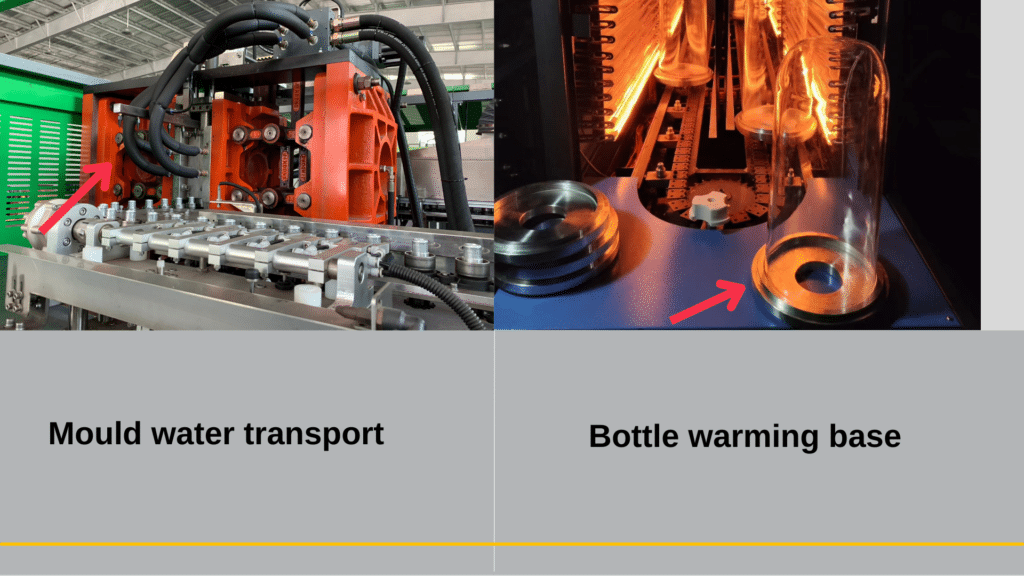
Conclusion: Work with Experienced Mold Manufacturers to Ensure Seamless Production
The precision of mold dimensions is crucial for production efficiency. Selecting an experienced mold manufacturer and securing detailed mold installation drawings and precise data before production helps avoid mismatched dimensions and related production issues. As a manufacturer with 20 years of expertise, we provide comprehensive support, from drawings to production, ensuring seamless mold-to-machine integration and efficient production.
For more professional mold information, please visit our website:http://www.ibottler.com