Customized PET preform mold
One-stop solution
- Soda bottle preform mold

- Neck Diameter: 28mm (Standard PCO1810, PCO1881), 30mm, etc.
- Weight Range: 10g – 50g, commonly used for 500mL, 1.5L, and 5L water and carbonated beverage bottles.
- Water bottle preform mold

- Neck Diameter: 28mm (Standard PCO1810, PCO1881), 30mm, etc.
- Weight Range: 8g – 50g, commonly used for 500mL, 1.5L, and 5L water bottles and beverage bottles.
- Daily chemical bottle mould
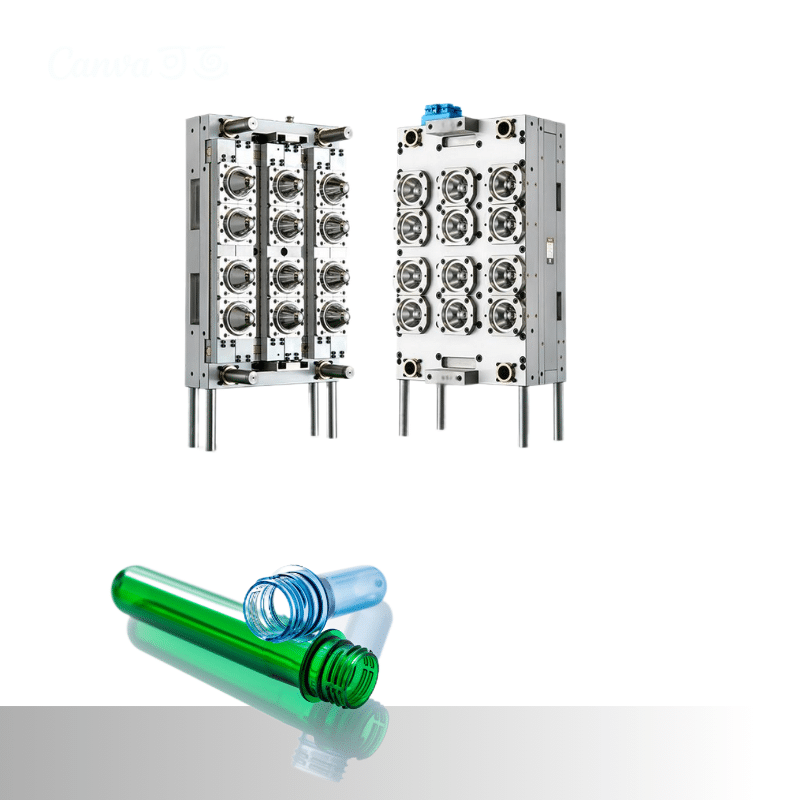
- Neck Diameter: 20mm, 24mm, 28mm, 38mm, customizable for pump or spray heads.
- Weight Range: 6g – 80g, applicable for 10mL – 2L Plastic bottles for detergent and cosmetic packaging.
- Five-gallon barrel mold
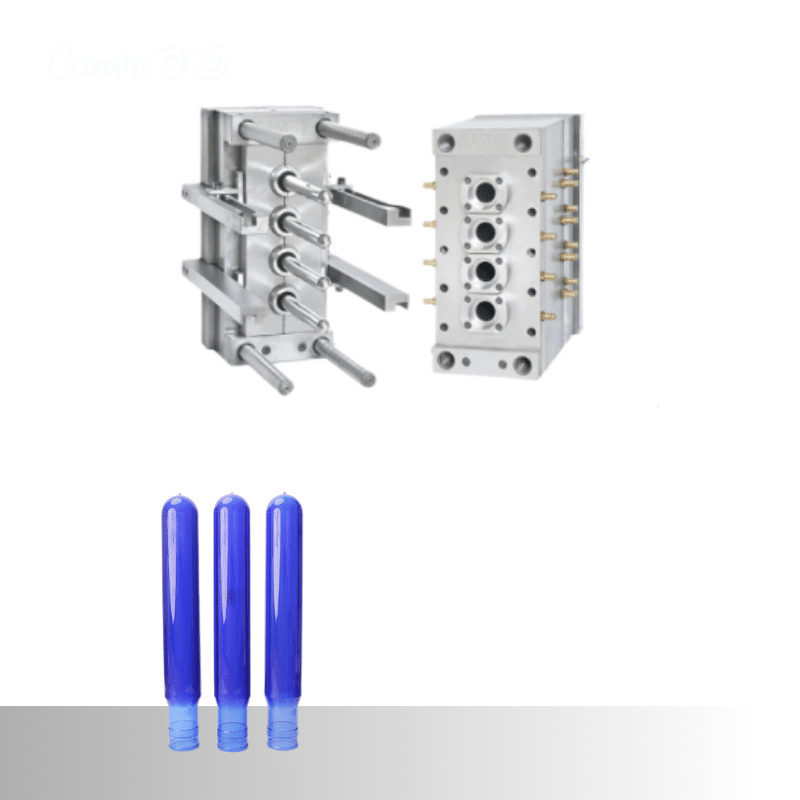
- Neck Diameter: 55mm (Standard 3-5 gallon neck size)
- Weight Range: 500g – 750g, suitable for 18.9L and 11.3L,large-capacity water bottles.
- Oil bottle preform mold
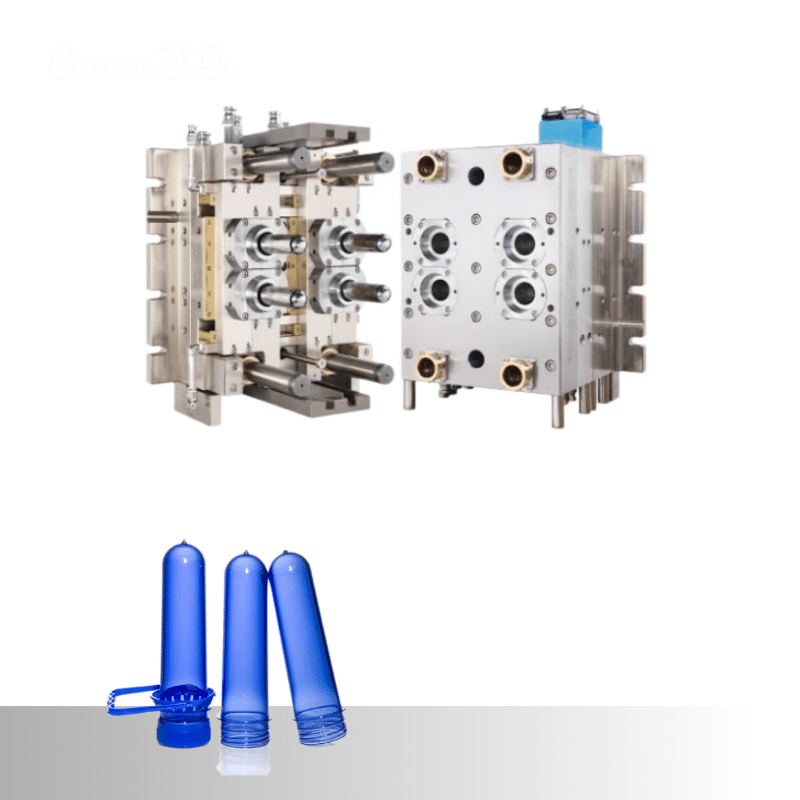
- Neck Diameter: 32mm, 45mm, 55mm, designed for oil product filling standards.
- Weight Range: 50g – 200g, suitable for 1L – 20L edible oil and lubricant containers.
- Wide Mouth Jar Mould
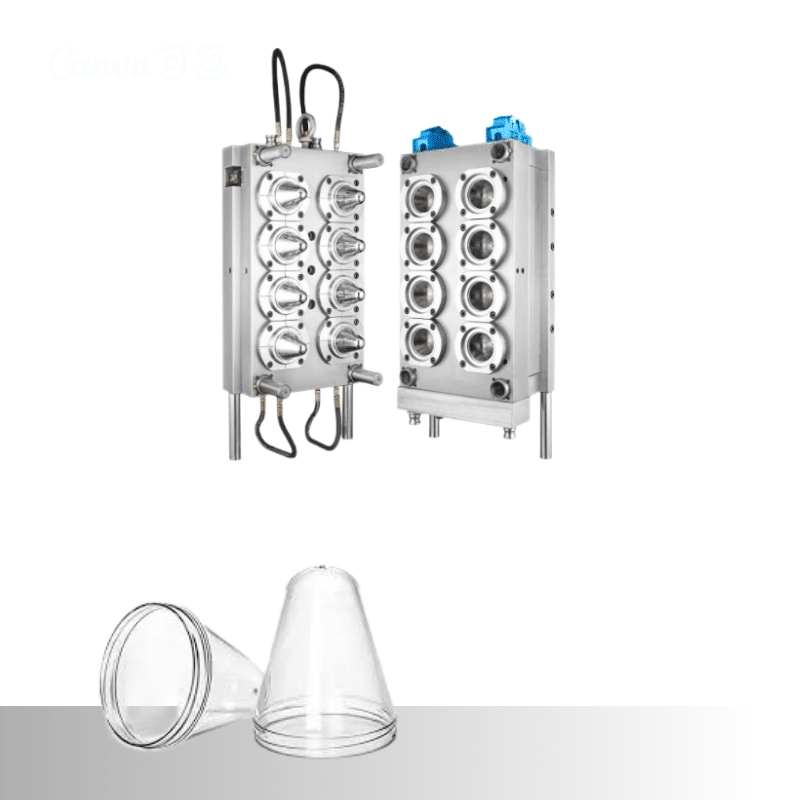
- Neck Diameter: 38mm, 45mm, 63mm, 83mm, suitable for large-diameter storage.
- Weight Range: 20g – 150g, compatible with 500mL – 5L large-volume containers.